A stalling automation transformation: Why do only 6 percent of warehouses use AGVs?
Limitations of legacy automation technologies are setting the logistics industry back. The Sevensense Visual SLAM solution is optimal for dynamic spaces and can easily be integrated into any vehicle platform, giving their manufacturers access to the 94% of warehouses currently untapped by automation.
Request A Meeting
Please fill out your details below. Our team will reach out to you by email to schedule a date and time.
Warehouse automation situation
No one argues against the potential benefits that automation can bring to the logistic operations.
There is consensus across the industry that automated material handling and transport will: increase efficiency, profitability, safety, and robustness to labor fluctuations.
Still, according to a G2 report, only 6% of warehouses used automated guided vehicles (AGVs) in 2021.
This number is extremely low. Why do 94% of today's warehouses still rely on manually operated vehicles?
The limitations of legacy automation technologies play a crucial role in answering this question.
A technological mismatch
Up until today, automated guided vehicles -AGVs- either use fixed floor installations such as rails and magnetic lines or vehicle-mounted laser scanners (so-called 2D LiDARs) for localization and navigation.
Both approaches can be effective in controlled, predictable, and static environments. However, logistics operations are often carried out under highly dynamic conditions.
Localization and navigation along magnetic lines
The automated vehicle centers itself against the line embedded into the floor and follows it during its operation. Beacons at intersections tell the vehicle which turn to take. The progression along a line is estimated based on the velocity of the vehicle.
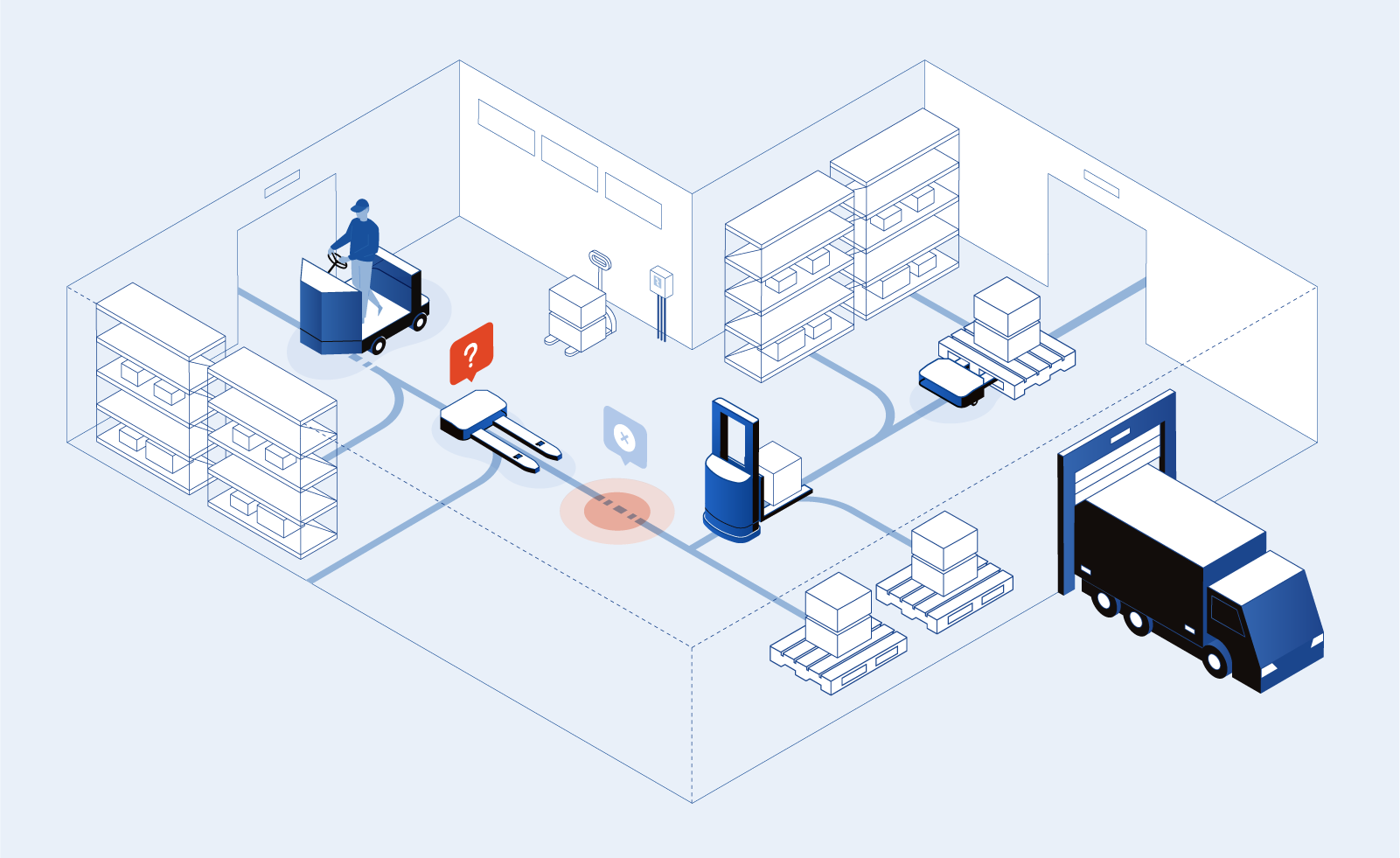
Limitations:
- An entire warehouse needs to be equipped with magnetic lines, which amounts to very significant planning and infrastructure costs, as well as downtimes during the installation.
- Once the lines are set up, automated vehicles can only ever navigate along these lines. While the operation is rather robust, it is extremely inflexible when it comes to major layout changes.
- Warehouses are traversed by heavy equipment, which will induce wear and tear on the magnetic lines. Hence, their maintenance is associated with high annual expenses.
Localization and navigation using 2D laser scanners
The laser scanner mounted on a vehicle can either detect special reflectors mounted in the operating environment or reflect off of natural features in the warehouse (e.g., walls, racks, pallets, boxes, other vehicles). The robot uses the distance and angle of the reflected beams to calculate its position and orientation in the environment.
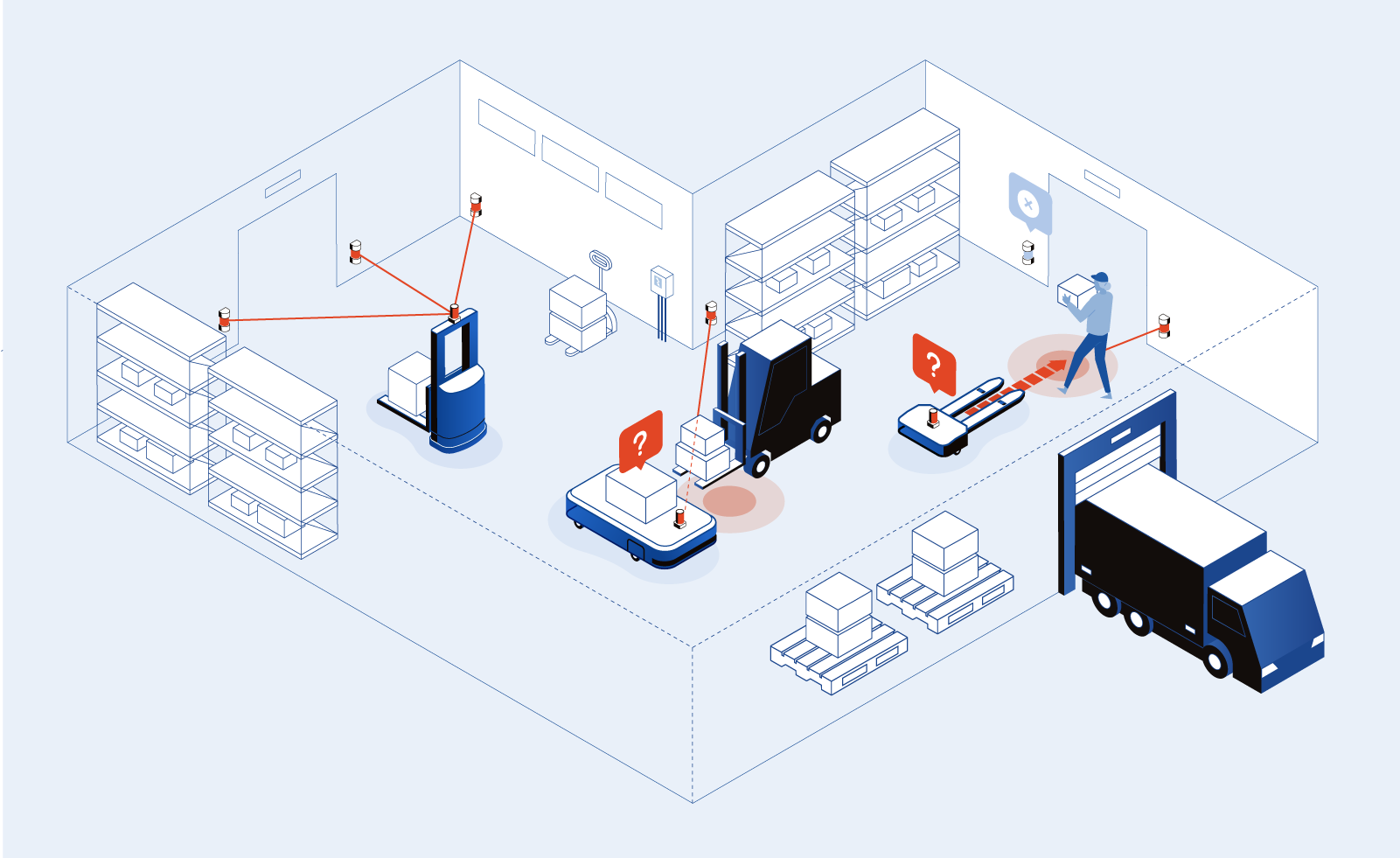
Limitations:
- When relying on reflectors, they must be mounted precisely throughout the entire facility, which is time-consuming and expensive. Their position also has to be kept fixed, and in case of layout changes, the whole setup has to be adapted.
- The vehicles need to have a clear line of sight to the reflectors, which can be obstructed by warehouse vehicles, products, or people. Crowded spaces are challenging.
- When relying on natural features, they shall only originate from permanent, static infrastructure such as walls and racks. Dynamic, movable obstacles such as pallets, carts, boxes, humans, and other vehicles must be removed manually from the map of the environment. Furthermore, their presence has to be reduced to an absolute minimum during operation to prevent AGVs from getting lost.
- Floors need to be even in order to precisely navigate, as the 2D laser scanners rely on the assumption that the operating space is completely flat. Consequently, vehicles cannot operate on ramps or uneven floors. Very large, open spaces -like logistics yards-, where reference objects are located several meters away from each other, are also not reliably handled by laser scanners.
A logistics-suited approach: Visual SLAM localization and navigation
Visual SLAM (Simultaneous Localization and Mapping) is a positioning and navigation technology that uses cameras and additional sensors to perceive the environment. The system uses computer vision algorithms and machine learning techniques to detect and track distinctive visual features such as corners, edges, and objects to build a rich 3D map of the environment and to estimate the position and orientation of the robot in real-time.
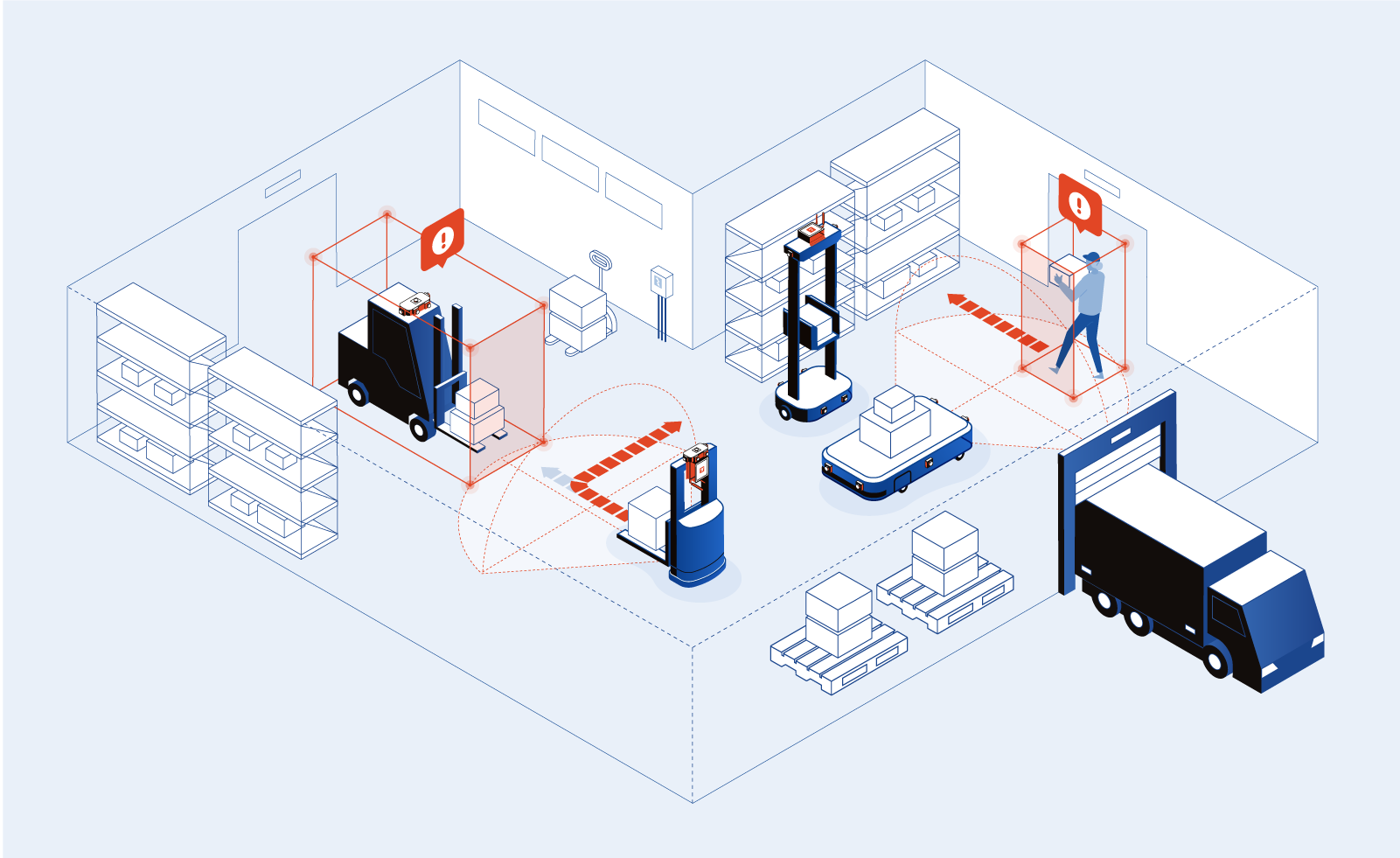
Advantages:
- This method does not require any costly infrastructure installations; the environment is perceived as it is.
- Thanks to AI-powered map learning, the technology is highly flexible and can work in dynamic environments such as warehouses where the layout may change frequently.
- The extracted visual features contain much more information compared to 2D laser natural features and reflector points (e.g. intensity, contrast, shape), which greatly enhances the robustness of the localization. Features will no longer be confused for one another.
- Since the map is built-in 3D and not 2D, the technology allows robots to navigate precisely on ramps and uneven floors. Moreover, the number of extracted features is orders of magnitude higher, which opens the possibility to flexibly change and reconfigure parts of the environment.
- The robots can work alongside humans and moving objects, as the technology is less sensitive to occlusions and can detect and avoid people and objects.
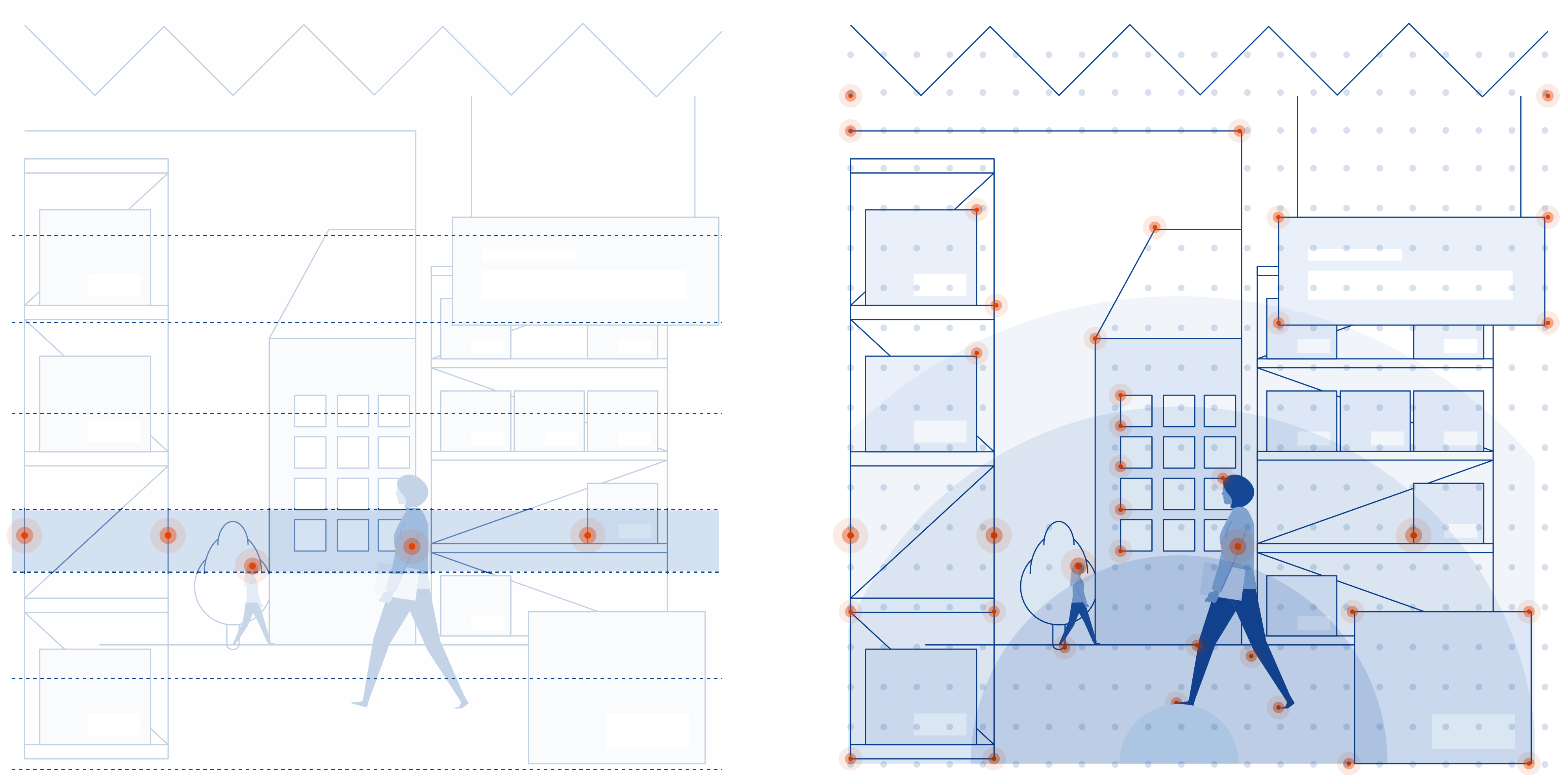
Overall, Visual SLAM technology offers a more flexible and adaptable solution for navigating complex and dynamic environments such as warehouses where products are moved around regularly, making it an ideal choice for the logistics industry.
According to the DHL Logistics Trend Radar, sales of mobile robots in the logistics industry are expected to grow by 31% per year between 2020 and 2023. This growth is facilitated by a technology shift from 2D LiDAR autonomy (based on Laser scanners) to 3D Visual SLAM autonomy, which is significantly advancing mobile robots in various applications and boosting their uptake. DHL visualizes this immense technology potential of 3D visual autonomy through the graph below:
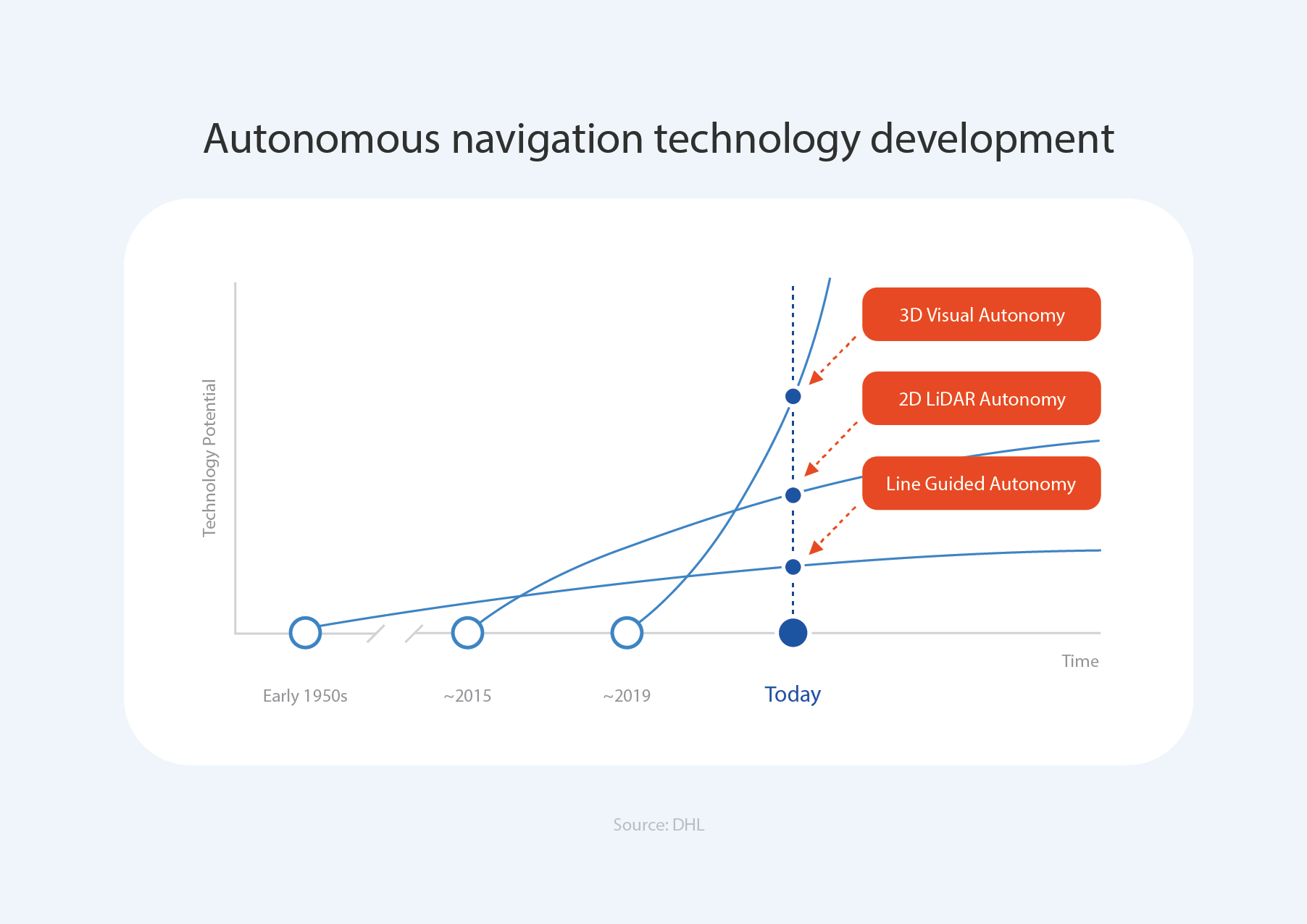
“Today, we are seeing more and more applications for indoor mobile robots in logistics. Especially in markets with higher labor costs, indoor mobile robots are being used extensively in order fulfillment. In other areas such as automated mobile manipulation, however, the technology is not yet widely marketable and will take a few more years to achieve commercialization on an industry-wide level. As soon as indoor mobile robots can be deployed at scale, they have enormous potential to reduce cost and increase efficiency within operations. Therefore, this trend is considered highly impactful for the logistics industry.” DHL Logistics Trend Radar 6.0: Indoor Mobile Robots
Before introducing Sevensense’s Visual SLAM solution, the technology was considered pre-mature and experimental.
ABB Robotics and the jury of the Swiss Technology Award agree that Sevensense has successfully elevated Visual SLAM to an industrial grade.
Alphasense: Industrial-grade Visual SLAM localization and navigation system
Sevensense Robotics provides the first and only industrial-grade visual navigation solution for autonomous robots - combining the required hardware and software in a single product.
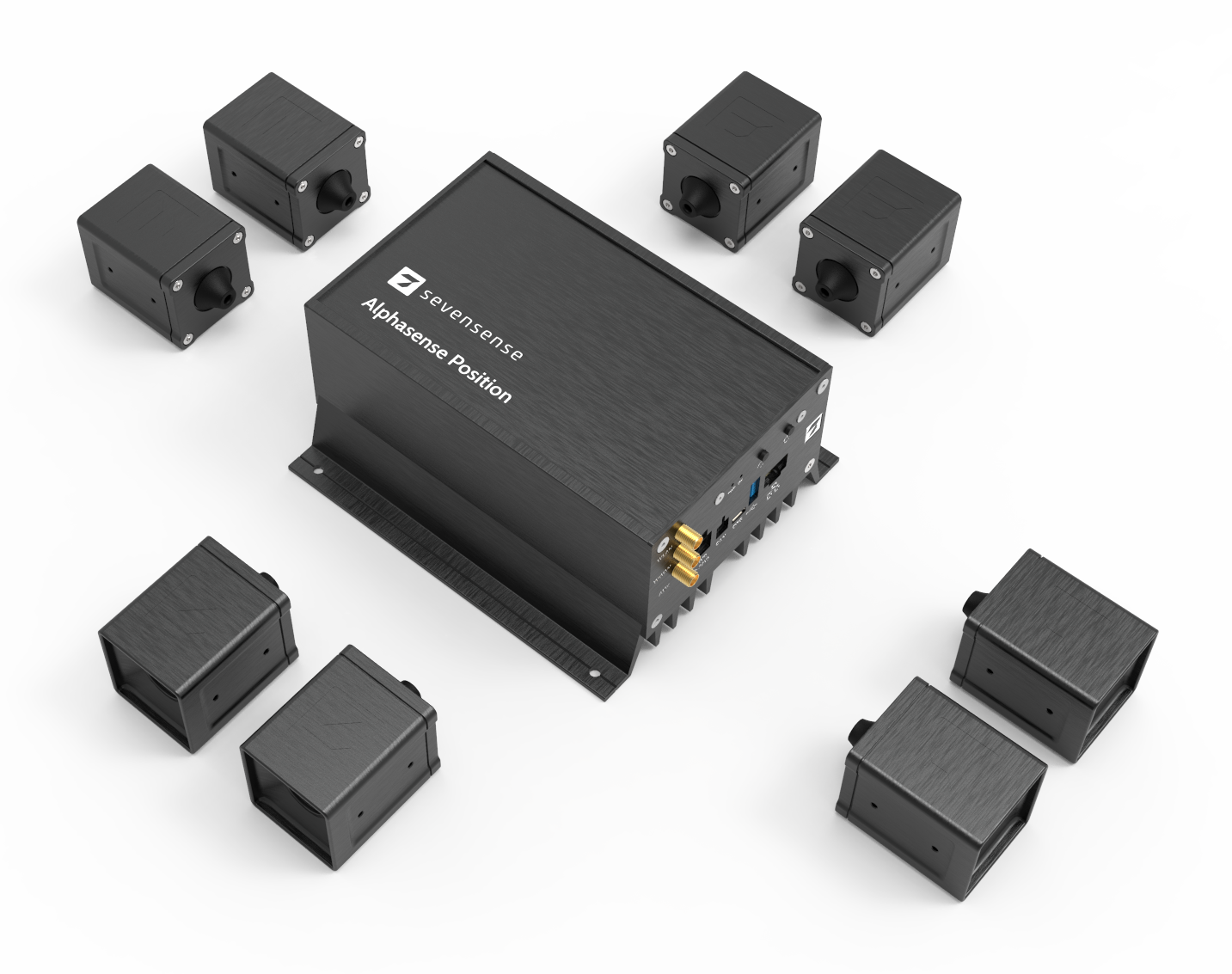
It is a plug-and-play solution to make any robot autonomous. The hardware of our product consists of a compute unit that runs our algorithms and the cameras that perceive the environment. Customers can place the cameras anywhere on their robot, allowing for maximum integration flexibility.
The tight integration of the hardware and software is critical for optimal performance of the underlying compute algorithms. Careful tuning of these two components gives Sevensense a unique advantage over competing software-only solutions.
Alongside the hardware, we provide two different software solutions: “Alphasense Position” allows any robot to reliably localize itself with millimeter-level accuracy. This level of accuracy is revolutionary in the mobile robotics industry.
Once a robot knows its location, our “Alphasense Autonomy” software adds another layer of intelligence that navigates a robot from A to B while detecting and avoiding obstacles, dynamically planning the path depending on the traffic and reacting to people or objects around the vehicle by our Visual AI.
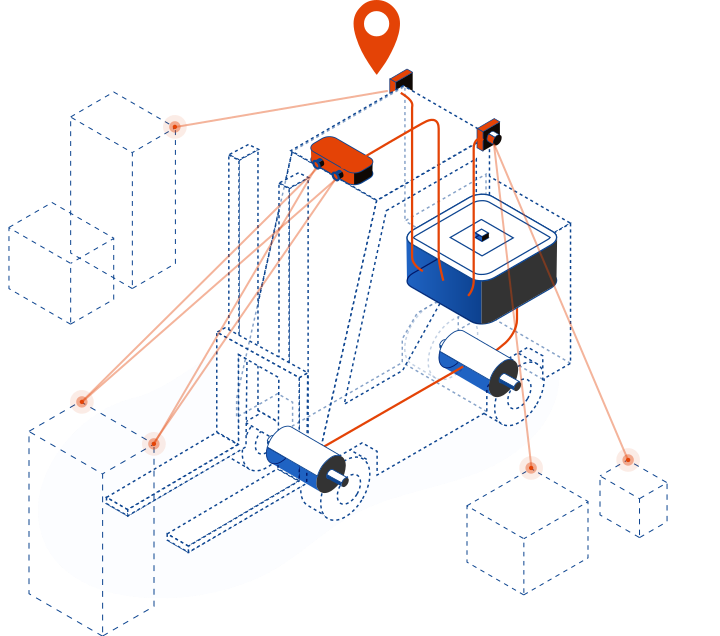
Closing the technological gap
With its unique market-proven Visual SLAM technology, Sevensense enables any provider of manually operated vehicles to become a manufacturer of smart mobile robots. Our solution can easily be integrated into any vehicle platform, giving their manufacturers access to the 94% of warehouses currently untapped by automation.
Millions of forklifts (1.5 M sold annually according to the Industrial Truck Association) and other logistic vehicles - such as tuggers and pallet trucks - can now be automated without years of costly developments.
Sevensense is enabling the acceleration of warehouse and logistics operations automation, giving the industry the right technology to flexibly adapt and face current and future challenges.
Get in touch to learn more about the Alphasense technology